What is OEM? Key Things to Know About OEM Products
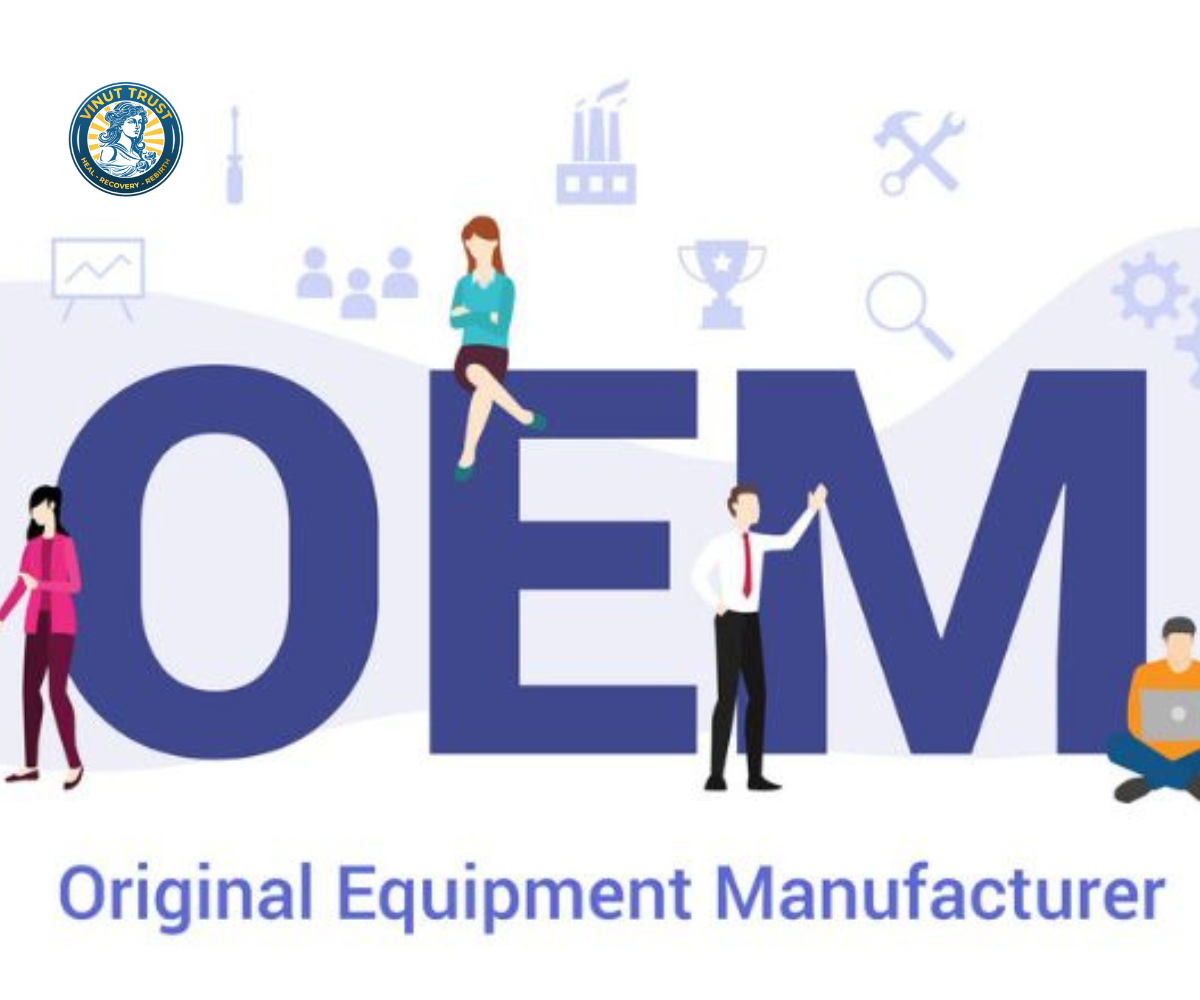
Mục lục
1. What Does OEM Stand For?
OEM (Original Equipment Manufacturer) refers to a company that designs and manufactures products or components that are then sold to another company. The end product is typically sold under the second company's brand name, rather than the manufacturer’s. In other words, an OEM creates products for another company to resell or rebrand.
To better understand, let’s break down the terms:
- Original: Refers to the fact that the equipment is created by the manufacturer.
- Equipment: Denotes the actual product, whether it be hardware, software, or any other goods.
- Manufacturer: The company that builds the product.
For example, consider the smartphone industry. While companies like Apple, Samsung, and Google sell smartphones under their own brand names, many of these smartphones are made using components or even entirely manufactured by third-party OEMs, such as Foxconn or Qualcomm.
2. OEM in Different Industries
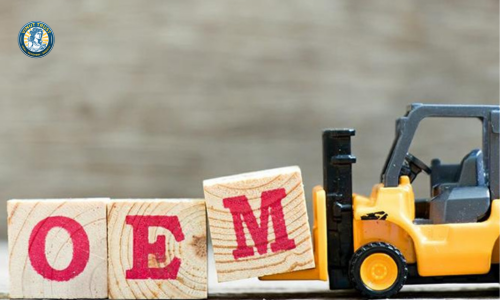
OEM products are prevalent in various industries, including:
- Automotive Industry: Car manufacturers rely on OEM parts for production and replacements. For example, Toyota may source certain car parts like headlights or engines from OEM suppliers.
- Technology: In tech, companies like Apple and Microsoft often use OEMs for components like processors, screens, or even complete laptops or mobile phones.
- Healthcare: Medical equipment and devices are often made by OEMs and then branded by healthcare companies or hospitals.
- Consumer Electronics: Many consumer electronics, such as TVs, laptops, and other home appliances, use OEM parts or entire systems manufactured by third parties.
3. Advantages of OEM Products
The decision to use OEM products can provide various advantages for businesses, especially when it comes to cost and efficiency. Here are some key benefits:
1. Cost-Effective Solutions
One of the main reasons companies turn to OEM products is cost efficiency. By outsourcing production to an OEM, companies can avoid the costs associated with setting up and maintaining a manufacturing facility. This also saves on labor costs, especially when OEM suppliers are based in countries with lower production expenses.
Example: A tech company may not have the resources to manufacture high-quality computer chips in-house. Instead, they may choose to source these chips from an established OEM like Intel or AMD, which allows them to save money and focus their resources on other aspects of their business, such as marketing and software development.
2. High Quality and Reliability
Many OEMs are established companies with decades of experience and expertise in their specific fields. Their manufacturing processes are often highly refined, meaning that their products are typically of high quality. In many cases, OEMs use the same parts and components that are used in original products, ensuring that the end product has the same quality and functionality as a company’s in-house-produced item.
Example: Car manufacturers often rely on OEM suppliers for critical components like brake systems, engines, and safety equipment. This ensures that the vehicle operates at the same level of reliability as the original equipment, reducing the risk of failure.
3. Time Savings
OEM partnerships allow companies to bring products to market more quickly. Since the OEM already has the necessary infrastructure, resources, and expertise, they can produce parts or products faster than a company could on its own. This means that businesses can focus on their core competencies, such as design, marketing, and customer service, rather than dealing with the complexities of manufacturing.
4. Customization and Flexibility
OEMs are often open to customization requests, allowing companies to tailor the product to their specific needs. Whether it’s adjusting the dimensions of a component, altering the material, or modifying design elements, businesses can often work with OEMs to get exactly what they want.
This flexibility can be especially valuable in industries such as tech or automotive, where small changes in design can make a significant difference in product performance.
5. Consistency and Scalability
OEMs can provide consistent product quality, which is essential for businesses looking to maintain their brand image. By working with a reliable OEM, companies ensure that all units produced will meet the same standards, regardless of how large or small the order is. Furthermore, OEMs are typically equipped to scale production up or down depending on demand, making it easier for businesses to adjust production levels as needed.
4. Disadvantages of OEM Products
While there are many advantages to using OEM products, there are also some disadvantages that businesses must consider. Let’s take a look at the potential downsides of OEM partnerships.
1. Limited Control over Production
One of the biggest drawbacks of working with an OEM is the limited control you have over the production process. The company that outsources its manufacturing to an OEM may not have as much influence over quality control, production timelines, or design modifications. This can be especially concerning if the OEM is located in a different country with different regulations or standards.
Example: If an OEM supplier is responsible for producing thousands of parts for a smartphone and there’s a mistake in one batch, the company selling the phones may not have direct control over fixing the issue, leading to potential delays or quality issues.
2. Intellectual Property Risks
When working with an OEM, there’s a risk that proprietary designs or technology could be leaked, misused, or copied. Companies must ensure that strong non-disclosure agreements (NDAs) and intellectual property protections are in place to avoid losing control over their products.
Example: If a tech company shares its proprietary smartphone design with an OEM, the manufacturer might use that design to produce similar products for competitors, undermining the original brand's competitive advantage.
3. Quality Control Issues
Even though many OEMs maintain high-quality standards, there’s always a risk that quality control issues may arise. This could be due to miscommunication, poor practices by the OEM, or differences in manufacturing regulations between countries.
Example: If an OEM does not adhere to strict quality standards, there could be instances of faulty components being shipped, which can harm the brand's reputation and lead to costly recalls.
4. Over-reliance on Third-Party Manufacturers
Using OEMs creates a dependency on third-party manufacturers. If the OEM faces supply chain disruptions, quality control issues, or financial problems, your business could be directly affected.
Example: During the COVID-19 pandemic, many OEM suppliers faced delays in production due to supply chain interruptions. Companies relying heavily on these suppliers were forced to deal with production delays and lost revenue.
5. OEM vs. ODM: Key Differences
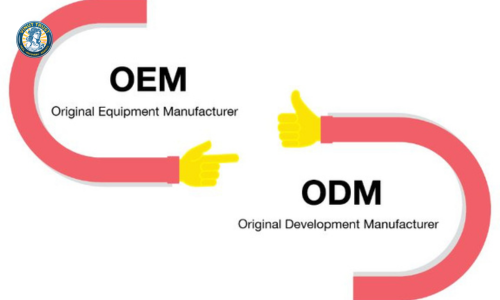
To fully understand the role of OEM, it’s helpful to compare it with another manufacturing model: ODM (Original Design Manufacturer). While OEMs manufacture products according to another company’s specifications, ODMs take it a step further by designing and manufacturing the entire product.
1. OEM (Original Equipment Manufacturer)
- What They Do: OEMs manufacture products or components as per a company’s design and specification, but the end product is typically branded by the company.
- Who Controls the Design: The company buying from the OEM controls the design and specifications.
2. ODM (Original Design Manufacturer)
- What They Do: ODMs handle both the design and manufacturing of the product. A company that works with an ODM typically doesn’t need to have an in-house design team.
- Who Controls the Design: The ODM controls the design, although the company purchasing the product may request modifications.
In summary, the primary difference between OEM and ODM is that OEMs produce existing designs, while ODMs create new designs.
6. OEM vs. Aftermarket Parts
Another comparison to consider is between OEM parts and Aftermarket parts. Aftermarket parts are produced by third-party manufacturers and are often sold as alternatives to OEM parts. Here’s a brief comparison:
- OEM Parts: Made by the original manufacturer or an authorized supplier, ensuring compatibility and original specifications.
- Aftermarket Parts: Manufactured by a third-party company and may vary in terms of quality, compatibility, and cost.
Benefits of Aftermarket Parts:
- Lower cost: Aftermarket parts can often be cheaper than OEM alternatives.
- Variety: You have more choices in terms of features and customization.
Risks of Aftermarket Parts:
- Incompatibility: Aftermarket parts may not always work well with the original equipment.
- Variable quality: The quality of aftermarket parts can be inconsistent, and you might face issues with performance or durability.
Conclusion: Is OEM Right for Your Business?
In conclusion, OEM products are an excellent option for many companies looking to reduce costs, maintain high-quality standards, and efficiently scale production. However, businesses should weigh the pros and cons, particularly in terms of control over design, intellectual property risks